Texturing nozzle spinning system
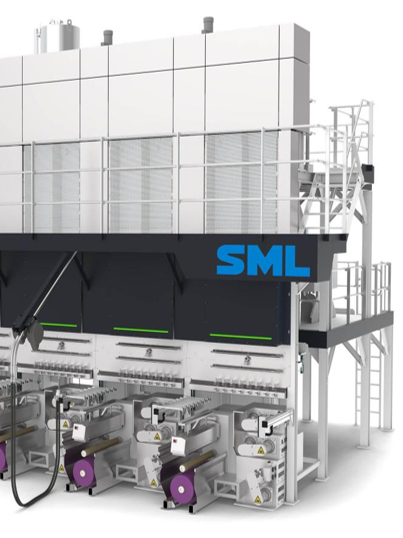
Faster production of multifilament threads thanks to simulation-based nozzle optimization
For the SML spinning system for the production of spun multifilament yarn, LCM has optimized the texturing nozzle as a critical component for increasing production speed. CFD simulations were used to analyze the existing nozzle geometry and a new Laval nozzle design was developed that enables an improved suction effect above the sound barrier. Prototype tests confirm a stable increase in production speed of 20% – limited only by other system components.
Initial situation and requirements
- Product of the system: spun multifilament thread
- Goal: Increase production speed
- Component: Texturing nozzle with suction effect using compressed air to tension the thread
- Problem: Air pressure is increased, but no increase in suction effect => production speed cannot be increased
Technology & results
- CFD simulation of the existing nozzle geometry
- Result: no exceeding of the sound limit possible => suction effect limited
- Redesign of the nozzle geometry (Laval nozzle) for optimum suction effect above the sound barrier
- Prototype tests show a stable increase in production speed of 20% (limited by other system components)
Dipl.-Ing., Dr. Markus Schörgenhumer, BSc
Business Area Manager Mechanics & ControlFurther reference projects
Automated measuring processes using cobots
Automated measuring processes using cobots Seamless combination of robotics and measurement technology A fully automated measurement process combines precise positioning,…
Automated sound intensity measurement
Automated sound intensity measurement Precise evaluation using sound pressure, sound intensity and sound power The system can be used to…
Self-sufficient sensor technology for rolling bearings
Self-sufficient sensor technology for rolling bearings Maintenance-free, wireless data acquisition Together with NKE Bearings, LCM has developed a technology that…