Digital hydraulic micropositioning system with high rigidity and accuracy
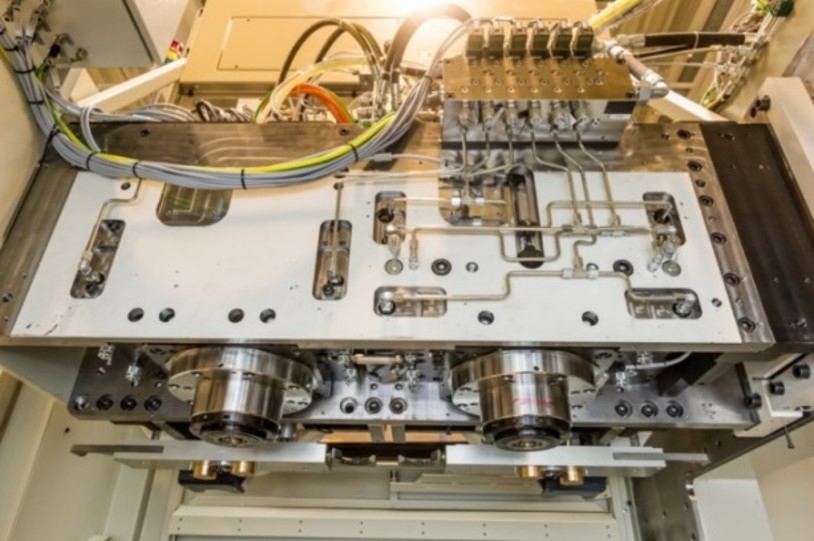
Frictionless positioning system with elastic diaphragms and digital valve control
This is a digital-hydraulic micropositioning system that is already used in machine tools. The objectives are high rigidity with very high positioning accuracy, dynamics and robustness of the system.
The adjustment range is approx. +/-100µm. The short stroke enables the use of elastic diaphragms, which are free of friction effects because they do not require sliding seals and can therefore be position-controlled much more precisely. The use of digital valves to control the required position also makes the system cost-effective and robust in terms of oil purity.
Control is via proportional control and an eddy current sensor; alternatively, the pressure difference can be used for lower accuracy requirements.
The system is compact, works almost friction and noise-free and requires only 0.16 liters of oil for over 10 minutes of operation. The advantages are high precision, dynamics, low costs and easy maintenance. Applications include precise positioning tasks, force and clamping control as well as travel control.
Requirements
- High positioning accuracy (< 1 µm)
- High rigidity of the system combined with short actuating travel
- Minimization of friction effects
- Robust function despite varying oil purity
- Compact, independent integration without central oil supply
Your benefit
- Eddy current sensor and proportional control enable
- Elastic diaphragms with digital control offer high rigidity with a short stroke.
- No seals means frictionless and more precise control.
- Digital switching valves regulate robustly and cost-effectively despite fluctuating oil purity.
- Low oil requirement and storage allow decentralized system integration
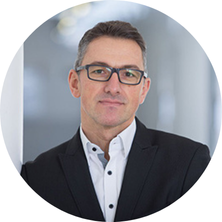
Bernd Winkler
Business Area Manager Hydraulic Drives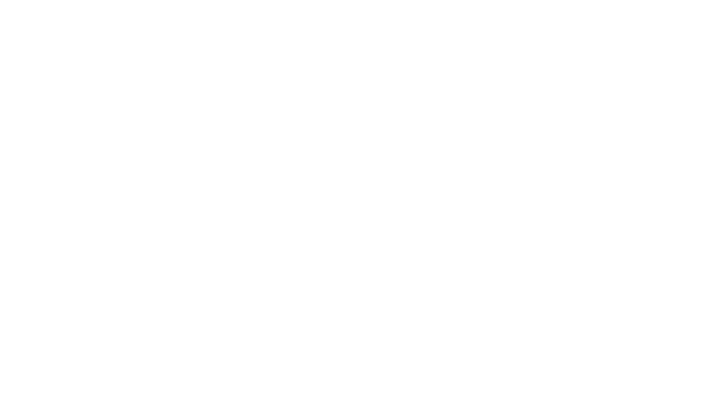
Further reference projects
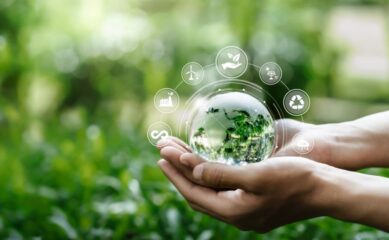
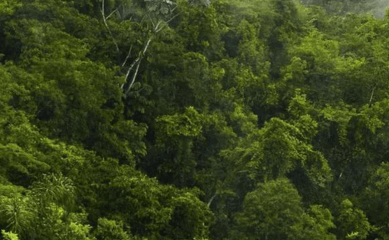
BABA emissions
BABA emissions BAtteria-Based energy storage for the mobile provision of EMISSION-free electrical energy The reduction of greenhouse gases (GHG) is…
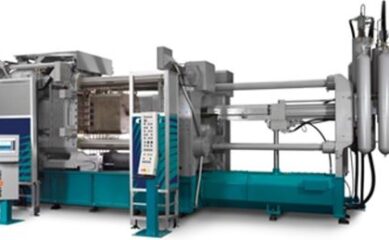
Smart Pump Management Die casting machine/Bühler
Less wear, more efficiency: retrofit solution for die casting systems during operation Smart pump management optimizes hydraulic systems in Bühler…