Quality assurance with vibration measurement
Faults are to be detected and classified on a ball bearing installed in a gearbox. The fault categories range from “faultless” to “slightly damaged” to “defective”. With the help of four key features, LCM’s solution delivers 99% correct fault detection!
Innovative solutions with AI
Artificial intelligence (AI) is currently on everyone’s lips. As your reliable research and development partner in the field of mechatronics, we at LCM offer our customers the opportunity to integrate AI into their products. This not only leads to increased efficiency, accuracy and robustness, but also gives you a decisive competitive advantage. AI opens up applications that would be unimaginable without this technology.
Find out how AI in an industrial context can revolutionize your business and how LCM can help you make the most of this transformative technology!
Definition of
“Artificial intelligence is the ability of a machine to imitate human abilities such as logical thinking, learning, planning and creativity. AI enables technical systems to perceive their environment, deal with what they perceive and solve problems in order to achieve a specific goal. The computer receives data (which has already been prepared or collected using its own sensors, for example a camera), processes it and reacts. AI systems are able to adapt their actions by analyzing the consequences of previous actions and working autonomously.”
(Source: EP).
Use of AI in the industrial environment
Integration of AI technologies with LCM
LCM supports you in the implementation of AI in your specific use case, especially in the area of condition monitoring. When a company brings a challenge to LCM, both the company and LCM usually have extensive technical knowledge of the system in question, also known as “domain knowledge”.
By using customized sensor technology, we first collect precise system data. At the same time, we offer the option of creating a computer model that can be used to simulate the system. The simulation generates additional data that can potentially represent undesirable operating conditions. The domain knowledge flows into both the data acquisition and the modeling & simulation.
The collected measurement and simulation data is then analyzed using AI algorithms to determine the current operating status of the component or machine, for example. Suitable actuators or measures are activated to ensure that the system is in optimum condition.
Use the advantages of LCM’s AI solutions for your company too!
Important terms
Machine Learning
Machine learning makes it possible to learn about a system based on data.
For example, if sufficient data from individual operating states is available, these states can be differentiated, e.g. for early detection of faults.
Common algorithmic approaches include supervised learning, unsupervised learning and reinforcement learning.
Digital twin
At LCM, the digital twin is not only composed of the CAD model, but also integrates the physical behavior and simulation of the entire model.
This comprehensive simulation enables data to be generated from operating states for which only limited measurement data is normally available, for example undesirable or rarely occurring operating states.
The digital twin thus helps to prevent operational downtimes.
Domain knowledge
Data can come from measuring devices or be generated by modeling the system and simulating it.
Existing knowledge about the system is incorporated into the modeling. This not only allows more data to be generated in general, but also allows operating states to be simulated that are unlikely to occur or should not occur at all during normal operation.
LCM AI solutions
In this section you will find a selection of implemented AI solutions from LCM.
Fault data without operational downtime
Specific fault data is essential for detecting faults in components, machines or systems. The simulation of various fault scenarios enables valuable data to be generated in order to avoid undesirable operating situations. Simulation data is particularly valuable for faults that never or only rarely occur and therefore make AI training more difficult.
Edwin Lughofer, Patrick Zorn and Edmund Marth, “Transfer learning of fuzzy classifiers for optimized joint representation of simulated and measured data in anomaly detection of motor phase currents,” Applied Soft Computing, Vol. 124, July 2022.
Monitor the service life of components
We have developed a digital twin specifically for predictive maintenance purposes. This enables us to effectively monitor and precisely calculate the remaining useful life of machine components such as bearings, actuators and clamping feet.
This digital twin is based on simulation results and can calculate non-measurable variables such as the development of contact pressure in the bearings during production. By combining virtual sensors and live measurements, we can track the wear of different parts and calculate their remaining useful life.
Monitor the service life of components
We have developed a digital twin specifically for predictive maintenance purposes. This enables us to effectively monitor and precisely calculate the remaining useful life of machine components such as bearings, actuators and clamping feet.
This digital twin is based on simulation results and can calculate non-measurable variables such as the development of contact pressure in the bearings during production. By combining virtual sensors and live measurements, we can track the wear of different parts and calculate their remaining useful life.
Sabrina Fleischanderl et al, “CNN-based crack detection in oxide layers of hot rolled steel sheet samples for the validation of a pickling process model”, Proc. 3rd Symp. on Pattern Recognition and Applications, 202
AI in practice: How and where to start?
Based on a study by McKinsey, the following steps can be taken to integrate AI into your own company:
The aim is not to replace people, but to support them in their work. This is precisely where AI unfolds its potential: by combining human knowledge with data-based methods.Veronika Putz Business Area Manager Sensors & Communication
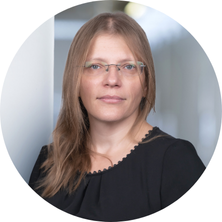
Veronika Putz
Business Area Manager Sensors & Communication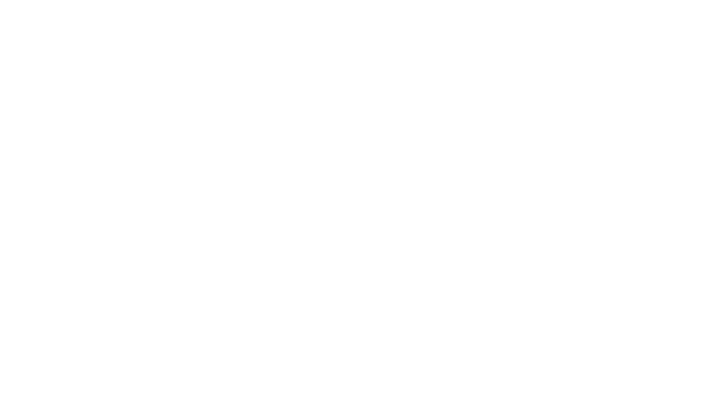